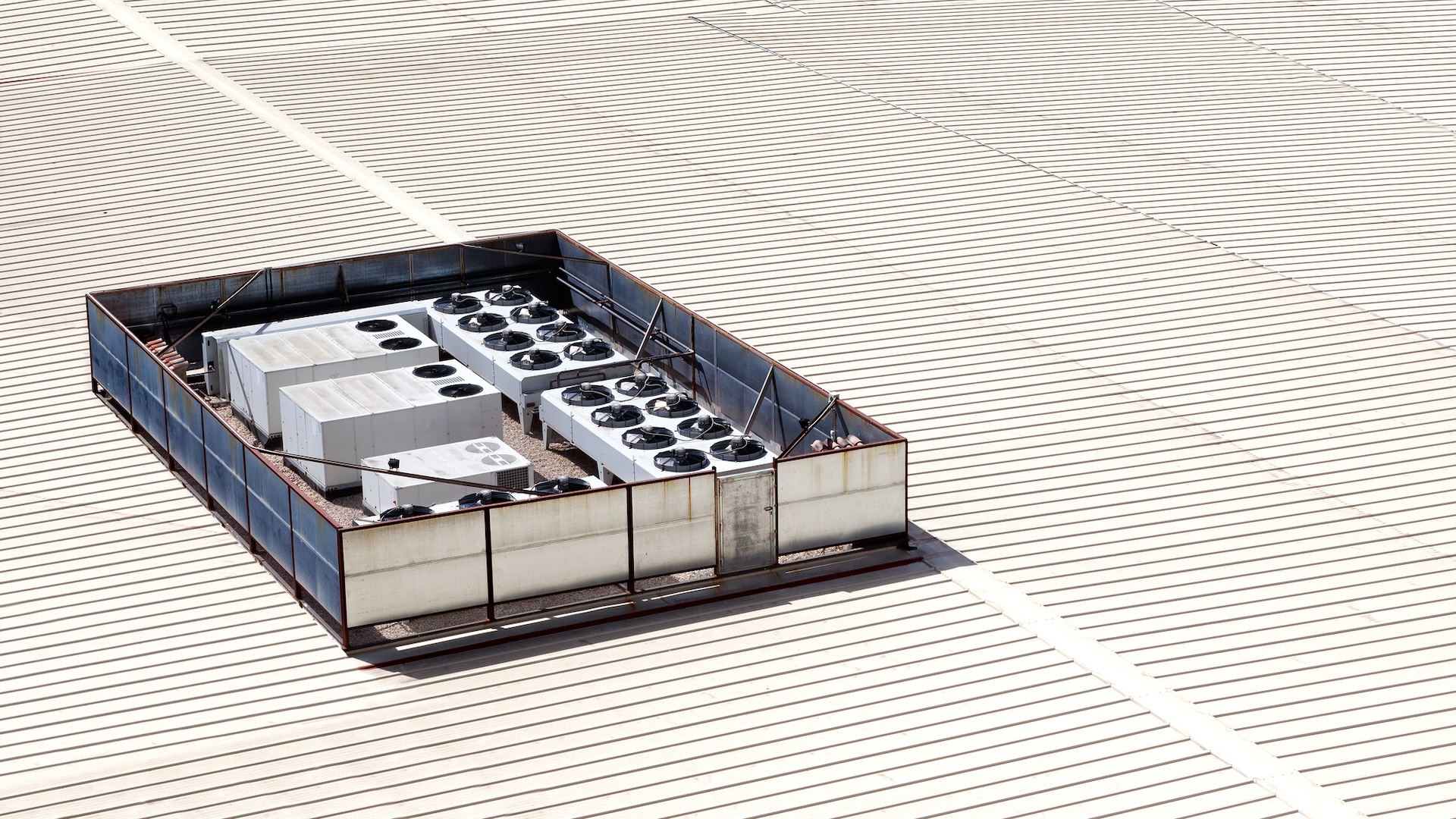
Building Owners and Managers: Know Your Roofing Systems
Most of us welcome the summer sun after a cold winter, but commercial building owners need to be attentive to the potential roof damage that can be caused by severe heat. Under normal conditions, Mother Nature is not always kind to flat roofs. Regular inspections are a cost-effective way to prevent big expenses due to weather damage.
Commercial roofs expand and contract in prolonged high temperatures, and any flat roof system is vulnerable to damage. While most roofing systems are designed to have some movement, extreme temperature swings put any roof to the test.
The best way for building owners to prevent expensive repairs is to know your roofing systems. Our advice is free, so it is critical to get out in front of potential problems.
An additional issue for commercial roofs in the Inland Northwest is the possibility of damage during fire season. TPO, PVC, and EPDM covered roofs, currently the most popular, are the roofing systems most prone to damage from embers or puncture from other windblown debris. When they are less than 15 years old, these roofs are also very repairable.
Metal roofs are the least vulnerable to weather damage and fire, but no roofing system is perfect.
Years ago, when most commercial flat roofs were shingles or built-up hot tar, the fix was typically applying more black tar over leaks caused by weather or fire damage. But, that is not a solution for TPO, PVC, or EPDM.
On TPO and PVC membrane roofing systems, SRC’s expert roofers restore a roof by cutting a section with clean margins around a leak. Next, they lay down plates in the affected area, clean, prime, and scrub around the plates, before finishing with a clean weld.
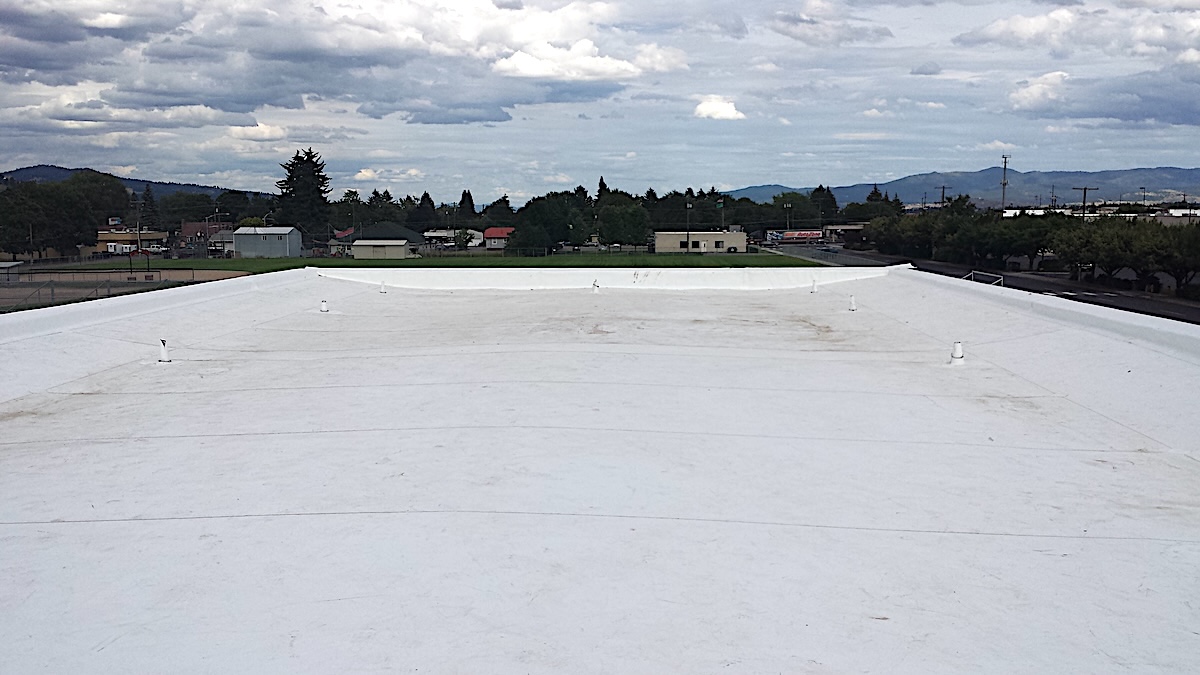
It is not a simple job,
says Sitton. You need specialized equipment and training to do it right. Only an insufficiently educated building owner or inexperienced roofing contractor will try to cut corners on roof leak repairs. When they do, problems usually resurface within 30 days, worse than when they started.
TPO is a good commercial roof, and it is the industry standard right now. Coatings are no longer required, compared to the old EPDM or hot tar roofs that needed recoating every two years.
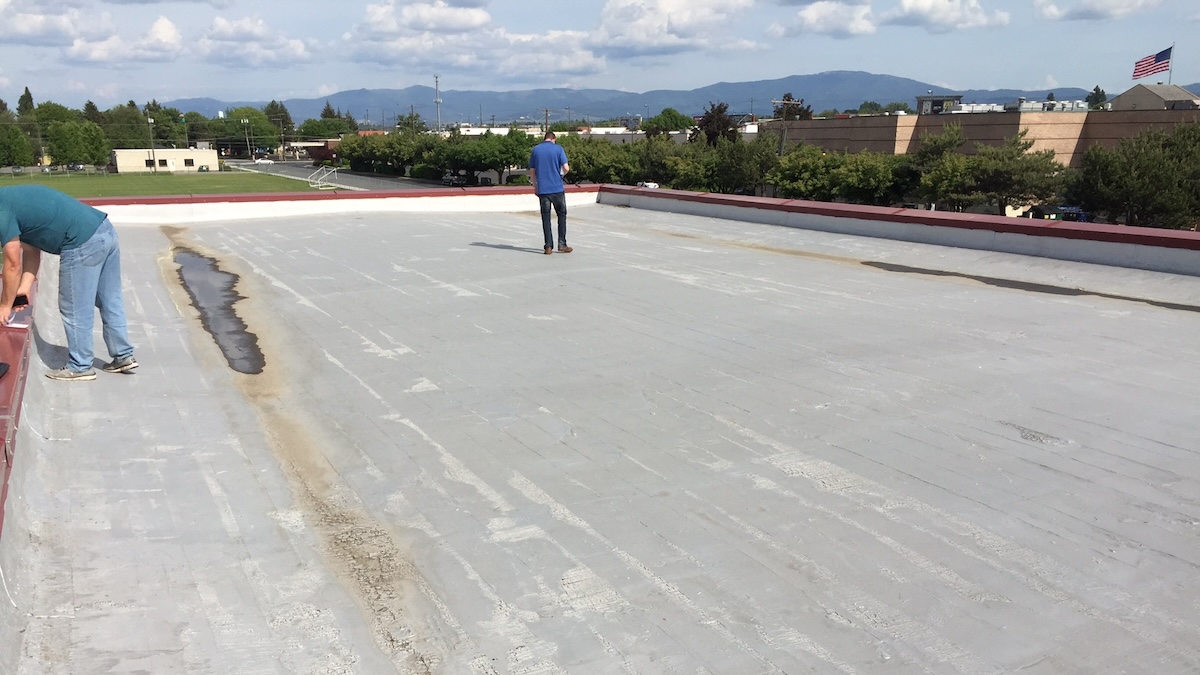
There is no perfect way to prevent damage to TPO, which is typically about 1/16-inch thick. An optional 1/8-inch thick TPO walkway offers more protection in high-traffic areas. While fire damage is rare, punctures created by blowing sticks and even pine needles are common. Most often, leaks develop from items dropped on the roof, especially punctures during HVAC equipment installation or repair.
A professional metal roof inspection includes checking screws and fasteners. They often pull loose due to abnormal movement caused by extreme weather, including high winds that get under sections of the roof.
Building Owner’s Best Friend
A reliable roofing contractor is a building owner’s best friend. Spokane Roofing Company offers regular inspections designed to detect roof damage from harsh weather conditions in both the winter and summer. Call Spokane Roofing today at (509) 838-8633 to speak with our friendly commercial roofing experts, schedule a free commercial roof inspection, or request a free estimate.
Citations
- Spokane Roofing Company – TPO Roofing Systems Guide – Building Owners
- Spokane Roofing Company – Commercial Metal Roofing Systems Guide – Building Owners
- Spokane Roofing Company – Commercial Flat And Metal Roof Maintenance.